Mastering DTF Printing: Tips and Tricks for Getting Vibrant and Resilient Prints
Worldwide of textile printing, accomplishing vibrant and resilient prints is a coveted skill that can raise the quality of your outcome. Understanding DTF (Straight to Film) printing requires a blend of technological knowledge, precision, and interest to information. From selecting the best products to fine-tuning print settings and developing post-printing finishing methods, there are many factors that can influence the result of your prints. Comprehending how to navigate these ins and outs can make all the distinction in between a mediocre result and a genuinely outstanding one.
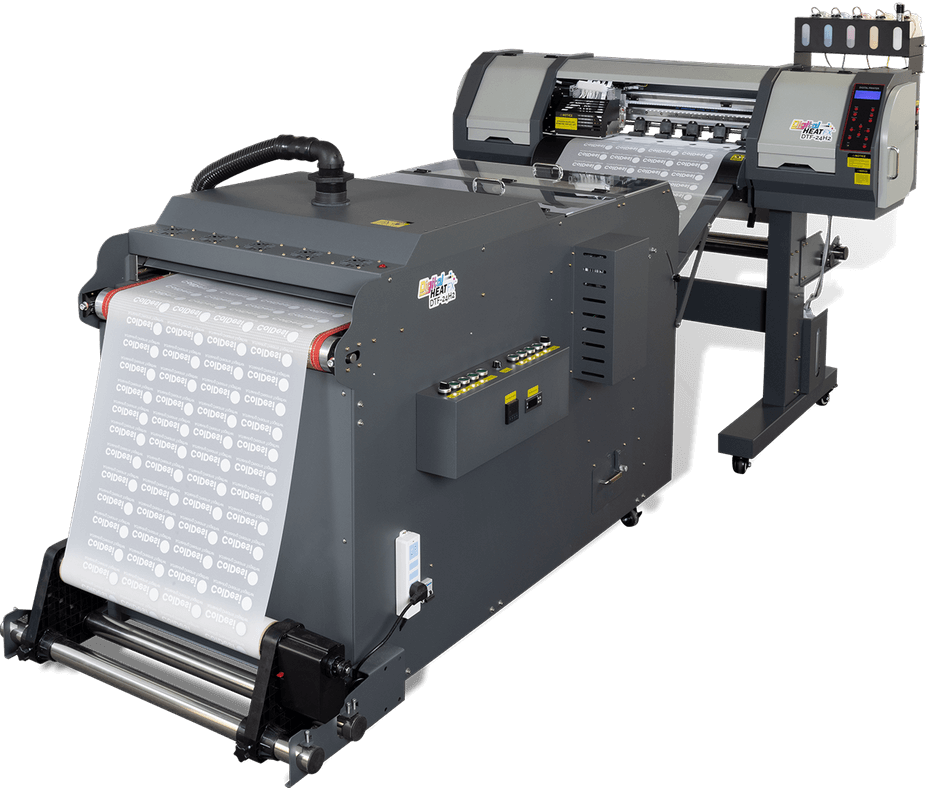
DTF Printing Fundamentals
For those new to the world of fabric printing, recognizing the basics of DTF printing is vital to grasping this ingenious method. Direct to Movie (DTF) printing is a contemporary method that involves moving styles from a special movie onto numerous textiles using a warmth press. Unlike standard methods like display printing, DTF uses advantages such as vivid shades, complex detailing, and the capacity to print on diverse products like cotton, polyester, and blends.
The process starts by printing the layout on an unique DTF film making use of a compatible printer with CMYK or CMYKW ink collections. When the design is published, it is after that cured with a warmth press to produce a long lasting and lasting print. DTF printing is known for its ability to reproduce intricate styles with high accuracy and color precision, making it a popular selection for services looking to produce personalized clothing, advertising items, and extra.
Choosing the Right Products

Just as vital is the option of the glue powder. The glue powder works as a bonding representative in between the published style and the textile, so it must have strong attachment residential properties to make sure a resilient and resilient transfer. Different fabrics may require various kinds of sticky powders, so it is important to match the powder to the fabric type for optimum outcomes - DTF Printing. By very carefully selecting the best materials for DTF printing, printers can boost the top quality, vibrancy, and durability of their prints.
Maximizing Print Setups
When intending to achieve the very best cause DTF printing, meticulous interest to optimizing print setups is essential for making certain exact and premium transfers onto textiles. When optimizing print setups is the resolution, one key element to consider. Greater resolutions typically cause sharper and a lot more detailed prints, improving the total high quality of the transfer. Additionally, readjusting the ink density can assist guarantee and achieve lively shades that the design sticks out on the textile.
While enhancing the speed can improve efficiency, it might endanger the last print's quality and shade saturation. Exploring with different speeds and observing the results can aid establish the ideal setting for each print job.
Additionally, tweak color accounts and making certain correct shade management are important for achieving regular and precise colors throughout different prints. By calibrating shade settings and accounts, printers can lessen shade discrepancies and create consistent results, improving the general print high quality and customer fulfillment.
Preparing Artwork for DTF Printing
Convert the artwork to CMYK color mode to make sure that the shades go to my site convert accurately from screen to print. Keep in mind to mirror the last layout before printing to guarantee that it transfers properly onto the garment. By adhering to these actions and paying close focus to the information, you can prepare art work that is optimized for vibrant and sturdy DTF prints.
Post-Printing Finishing Techniques
Executing effective post-printing finishing strategies is vital to improving the toughness and visual appeal of DTF prints on textiles. As soon as the printing procedure is total, applying warmth to the printed design is crucial.
When the film is eliminated, the print might need added curing time to better set the visit ink right into the fabric. This step assists enhance the washability and durability of the print, ensuring it can withstand several clean cycles without fading or breaking.
Furthermore, cutting any type of excess movie around the design can offer the final print a clean and specialist look. Putting in the time to properly finish DTF prints post-printing can dramatically impact the general high quality and long life of the textile design.
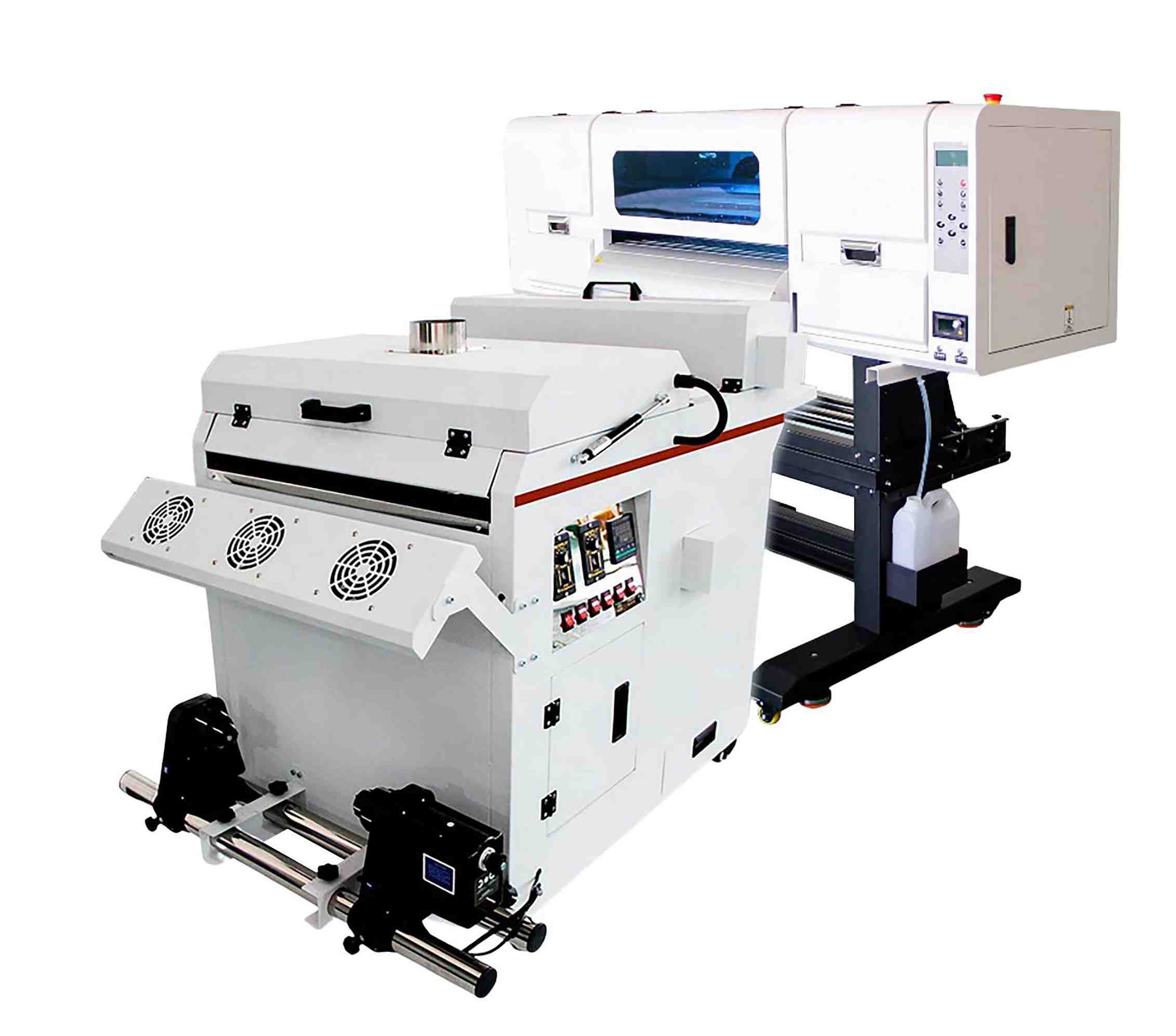
Verdict
To conclude, grasping DTF printing calls for a thorough understanding of the fundamentals, choosing ideal products, optimizing print settings, preparing artwork efficiently, and using post-printing ending up strategies. By adhering to these techniques and ideas, one can accomplish sturdy and lively prints that fulfill their wanted top quality criteria. Consistent technique and focus to information are essential in achieving successful outcomes in DTF printing.
From choosing the ideal products to adjust print setups and improving post-printing completing methods, there are many aspects that can affect the result of your prints. Unlike traditional approaches like display printing, DTF uses advantages such as dynamic colors, intricate describing, and the capacity to publish on diverse products like cotton, polyester, and blends.
Once the design is published, find out it is after that treated with a heat press to develop a sturdy and resilient print.When aiming to accomplish the finest results in DTF printing, thorough focus to enhancing print settings is essential for guaranteeing precise and high-quality transfers onto textiles.In final thought, grasping DTF printing requires a thorough understanding of the fundamentals, selecting ideal materials, maximizing print settings, preparing art work successfully, and utilizing post-printing ending up techniques.